解鎖高端裝備智造“卡脖子”局面,海目星制造執(zhí)行系統(tǒng)MES創(chuàng)新應(yīng)用
當(dāng)制造系統(tǒng)走進(jìn)鋰電工廠時(shí),它就扮演著一個(gè)極其重要的角色,能夠驅(qū)動(dòng)大規(guī)模制造轉(zhuǎn)向優(yōu)質(zhì)制造,自動(dòng)化生產(chǎn)升級(jí)到數(shù)字化生產(chǎn)。它將會(huì)像血管一樣,盤活整個(gè)鋰電池?cái)?shù)字工廠的生產(chǎn)生態(tài)。
鋰電工廠數(shù)字化轉(zhuǎn)型直面的“困局”
鋰電產(chǎn)業(yè)正邁向高質(zhì)量躍升發(fā)展的新階段,數(shù)字化、智能化轉(zhuǎn)型已是電池企業(yè)無法繞開的問題。但鋰電池生產(chǎn)周期相對(duì)較長、生產(chǎn)設(shè)備多、工藝復(fù)雜,從訂單到產(chǎn)品完成交付的整個(gè)生產(chǎn)活動(dòng),都面臨諸多棘手的難題和痛點(diǎn)。
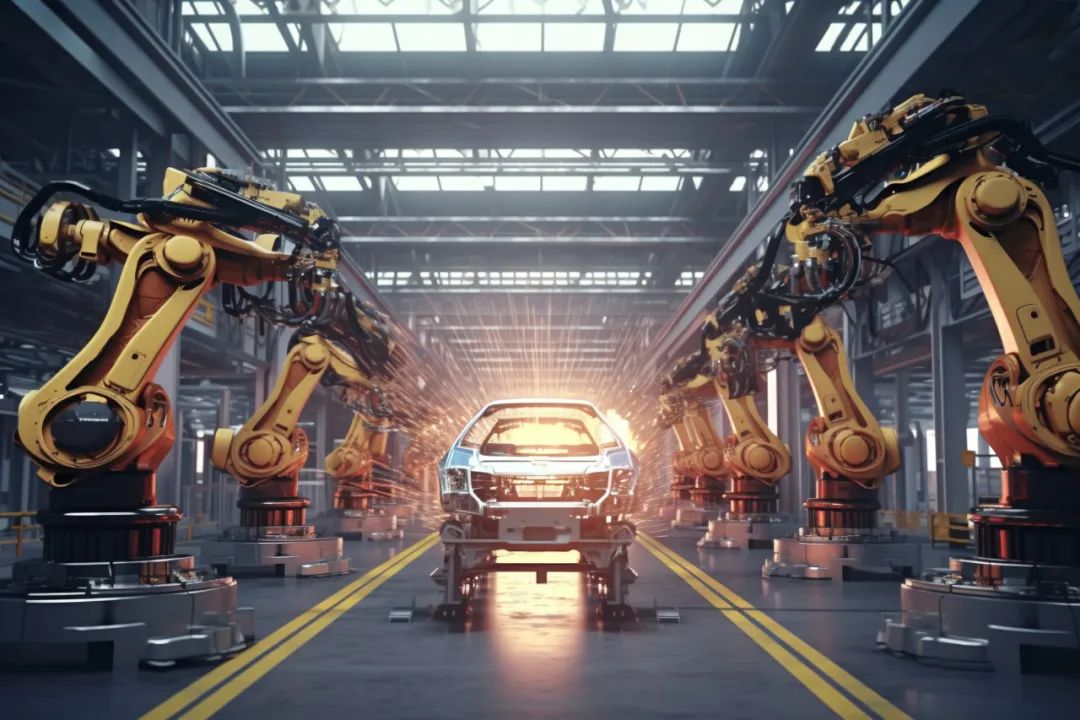
在生產(chǎn)管理方面,大規(guī)模制造背景下,電池企業(yè)對(duì)于資源調(diào)度、計(jì)劃排產(chǎn)、生產(chǎn)跟蹤、進(jìn)度管理、物料管理、存貨周轉(zhuǎn)等一系列環(huán)節(jié)提出了更精益、更敏捷的要求。
在設(shè)備管理方面,鋰電池制造過程涉及很多的自動(dòng)化裝備,設(shè)備實(shí)時(shí)運(yùn)行情況的獲取、工藝參數(shù)的管控及質(zhì)量數(shù)據(jù)的在線采集難度大。沒有實(shí)時(shí)精確的數(shù)據(jù),就無法發(fā)出正確的控制指令和生產(chǎn)指令,換型效率較低、庫存周轉(zhuǎn)率低下,全盤生產(chǎn)活動(dòng)無法迅速指導(dǎo)、反應(yīng)和報(bào)告。
在質(zhì)量管理方面,一方面缺乏規(guī)劃,基本追溯鏈斷裂;另一方面缺乏系統(tǒng)而完整的追溯方案,事后檢查模式質(zhì)量成本過高。
鋰電工廠要真正實(shí)現(xiàn)智能化、數(shù)字化并不是空中樓閣,需要通過切實(shí)可行的方式來解決這一系列的生產(chǎn)現(xiàn)場(chǎng)痛點(diǎn),為生產(chǎn)制造能力和產(chǎn)品競爭力的提升提供保障。
海目星制造執(zhí)行系統(tǒng)的應(yīng)用開發(fā)
海目星基于智能化、數(shù)字化工廠理念,結(jié)合鋰電池生產(chǎn)工藝特性、MES系統(tǒng)功能,同時(shí)導(dǎo)入制造及裝備主導(dǎo)的預(yù)測(cè)性的質(zhì)量管理、數(shù)字化的制造組織方式、數(shù)字化的計(jì)劃與物料管控解決方案,構(gòu)建全新的面向鋰電池生產(chǎn)的制造執(zhí)行系統(tǒng)MES。
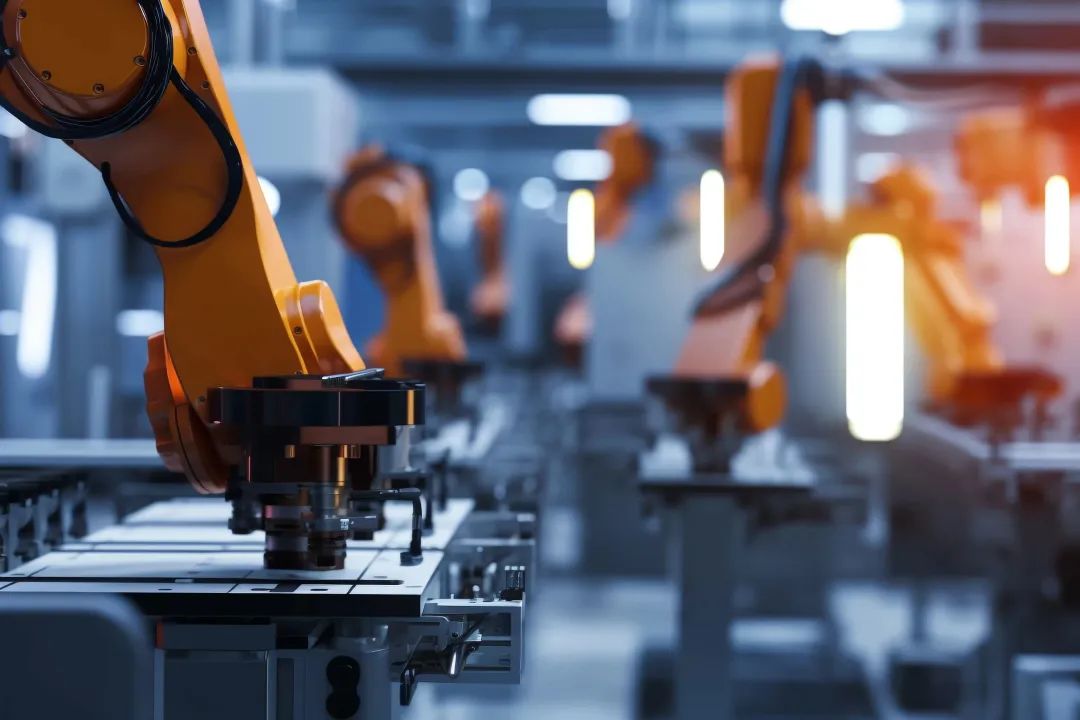
預(yù)測(cè)性的質(zhì)量管理解決方案
鋰電池制造工序繁多,節(jié)拍較快。例如組裝線產(chǎn)品檢測(cè)屬于后置工位,難以精確識(shí)別并有效隔離風(fēng)險(xiǎn)產(chǎn)品,單機(jī)異常后持續(xù)加工產(chǎn)生,最終導(dǎo)致批量的不合格產(chǎn)品,造成巨大的成本損失,極大地影響良品率。
通過MES構(gòu)建完整的追溯鏈解決方案,實(shí)時(shí)分析關(guān)鍵控制點(diǎn),做到毫秒級(jí)自動(dòng)響應(yīng);對(duì)異常設(shè)備發(fā)出“互鎖指令”,執(zhí)行反向控制 & 標(biāo)記分揀,防止不良品持續(xù)加工導(dǎo)致的浪費(fèi),某客戶8GWh產(chǎn)能工廠應(yīng)用后降本約800萬/年。
數(shù)字化的制造組織解決方案
在鋰電工廠的生產(chǎn)現(xiàn)場(chǎng),產(chǎn)品換型耗時(shí)長,逐臺(tái)設(shè)備重置參數(shù)工作量極大,短則一周,長則數(shù)月。另外配方版本多,換型容易出錯(cuò),易產(chǎn)生批量不合格產(chǎn)品。
通過MES統(tǒng)籌Recipe參數(shù)設(shè)置/配方設(shè)置,規(guī)范產(chǎn)品設(shè)計(jì)端和生產(chǎn)現(xiàn)場(chǎng)數(shù)據(jù)保持一致;快速實(shí)現(xiàn)產(chǎn)品換型,設(shè)備參數(shù)/產(chǎn)品配方一鍵下發(fā)至生產(chǎn)設(shè)備;再經(jīng)過Recipe參數(shù)校驗(yàn)+配方校驗(yàn),即可在生產(chǎn)過程中執(zhí)行。MES系統(tǒng)執(zhí)行的修改、審批,再重新同步,執(zhí)行,進(jìn)一步確保了工藝的規(guī)范性。
某客戶應(yīng)用海目星-數(shù)字化的制造組織解決方案,實(shí)現(xiàn)了單次換型標(biāo)準(zhǔn)調(diào)整時(shí)間縮短80%;另外防止因人工標(biāo)準(zhǔn)設(shè)定錯(cuò)誤導(dǎo)致的產(chǎn)品異常,隱形降本約100萬/年。
數(shù)字化的計(jì)劃與物料管控
針對(duì)WMS/MES/SAP未實(shí)現(xiàn)系統(tǒng)互通,造成多套賬,人工處理及時(shí)性和準(zhǔn)確性難度較大,另外現(xiàn)場(chǎng)人工巡檢物料狀態(tài),不能及時(shí)準(zhǔn)確反映線體物料需求,入賬需人工輸入,易漏錄、錯(cuò)錄。
通過MES與WMS系統(tǒng)集成,建立起物流、生產(chǎn)流、信息流互聯(lián)互通的管理平臺(tái)。實(shí)現(xiàn)物料需求與物料配送一體化,實(shí)現(xiàn)現(xiàn)場(chǎng)物料配送無紙化,提高數(shù)據(jù)流轉(zhuǎn)準(zhǔn)確性、完整性,現(xiàn)場(chǎng)工作效率提升。
同時(shí),提供了自動(dòng)報(bào)工與自動(dòng)排程支持,自動(dòng)統(tǒng)計(jì)良品/不合格品/報(bào)廢品,并上傳ERP;工序物料消耗自動(dòng)計(jì)算;報(bào)廢品精準(zhǔn)分類等。極大地解決了過去手工記賬人力消耗與數(shù)據(jù)準(zhǔn)確性問題,提高賬實(shí)一致率,減少盤點(diǎn)差異,支持財(cái)務(wù)進(jìn)一步地成本精細(xì)化管理。
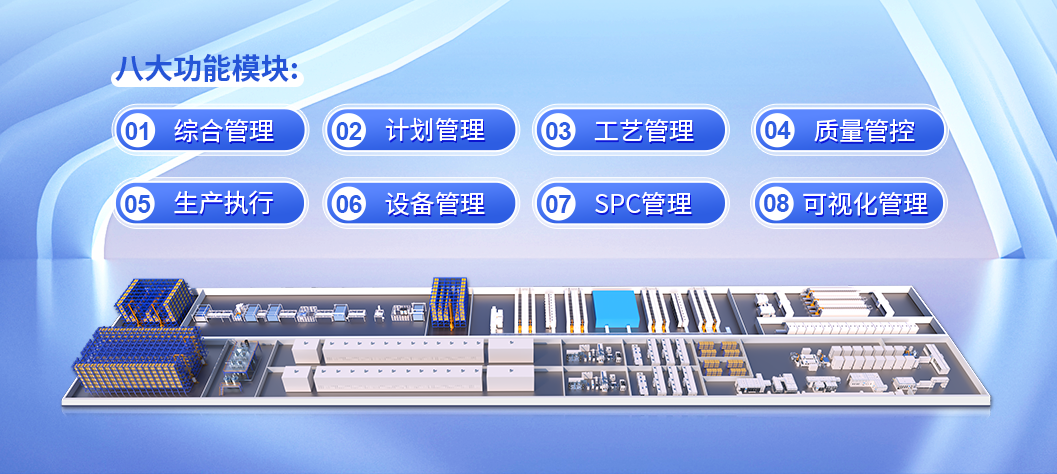
從鋰電池生產(chǎn)實(shí)際需要出發(fā),MES提供實(shí)現(xiàn)從漿料制造、極片制造、電芯制造、電芯測(cè)試、模組組裝(涵蓋CTP)的鋰電池生產(chǎn)全制程優(yōu)化所需的信息。聚焦綜合管理、計(jì)劃管理、工藝管理、質(zhì)量管控、生產(chǎn)執(zhí)行、設(shè)備管理、SPC管理、可視化管理等八大功能模塊,破解流程制造,批次管控問題,解決離散制造的不確定性及復(fù)雜性的難題,實(shí)現(xiàn)批量化、定制化的數(shù)字化精益生產(chǎn),降本增效,打造實(shí)時(shí)可視的數(shù)字化鋰電工廠!
海目星致力于為電池企業(yè)創(chuàng)造真正的價(jià)值,塑造綜合競爭能力。伴隨著TWH時(shí)代的到來,MES必然成為將賦能鋰電行業(yè)數(shù)字化升級(jí)的著落點(diǎn),幫助電池企業(yè)實(shí)現(xiàn)高投資回報(bào)率、高精益化、高智能化,讓企業(yè)以MES為伴,更好應(yīng)對(duì)鋰電產(chǎn)業(yè)的風(fēng)云變幻。
THE END